CAMBRIDGE, England, Aug. 29, 2022 — A machine learning algorithm developed by researchers at the University of Cambridge quickly detects and corrects 3D printing errors — even in previously unseen designs or unfamiliar materials. The algorithm can be easily added to new or existing machines to enhance their capabilities. 3D printers using the algorithm could also learn how to print new materials by themselves.
Although 3D printing holds immense potential for the production of complex and customized parts, structures, and even food, the technology is vulnerable to production errors, from small-scale inaccuracies and mechanical weaknesses to full structural failure.
At present, the way to prevent or correct these errors is for a skilled worker to observe the process. The worker must recognize an error, stop the print, remove the part, and adjust the settings to create a new part. Errors may be missed if there are multiple printers running simultaneously, particularly for long prints.
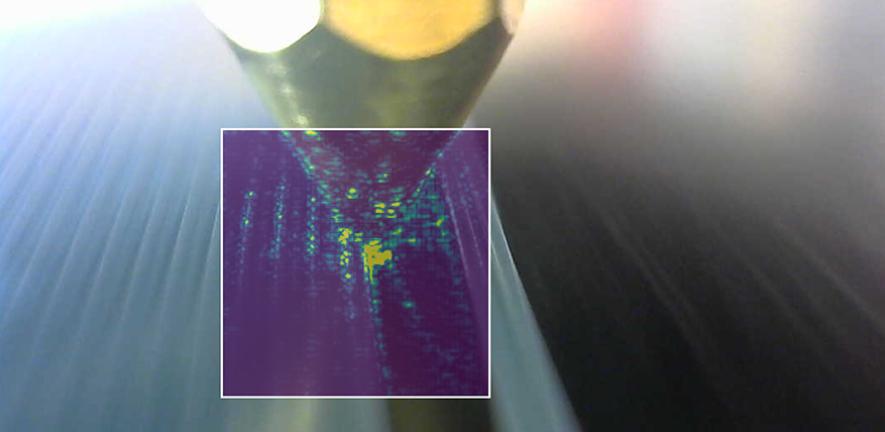
Example image of the 3D printer nozzle used by the machine learning algorithm to detect and correct errors in real time. Courtesy of Douglas Brion/University of Cambridge.
When 3D prints fail, said Sebastian Pattinson, a professor in the University of Cambridge’s Department of Engineering and a senior author on the paper, material, time, and energy are lost.
Engineers have been developing automated 3D printing monitoring. But existing systems can only detect a limited range of errors in one part, one material, and one printing system.
“What’s really needed is a ‘driverless car’ system for 3D printing,” said first author Douglas Brion, also from the Department of Engineering. “A driverless car would be useless if it only worked on one road or in one town — it needs to learn to generalize across different environments, cities, and even countries. Similarly, a ‘driverless’ printer must work for multiple parts, materials, and printing conditions.”
Brion and Pattinson said the developed algorithm could be the “driverless car” engineers have been looking for. “What this means is that you could have an algorithm that can look at all of the different printers that you’re operating, constantly monitoring and making changes as needed — basically doing what a human can’t do,” Pattinson said.
The researchers trained a deep learning computer vision model by showing it around 950,000 images captured automatically during the production of 192 printed objects. Each of the images was labeled with the printer’s settings, such as the speed and temperature of the printing nozzle and flow rate of the printing material. The model received information about how far those settings were from “good” values, allowing the algorithm to learn how errors arise.

The trained algorithm figured out just by looking at an image which setting was correct. It could also apply the appropriate correction.
“And the cool thing is that printers that use this approach could be continuously gathering data, so the algorithm could be continually improving as well,” Pattinson said.
The algorithm is generalizable — in other words, it can be applied to identify and correct errors in unfamiliar objects or materials, or even in new printing systems. “When you’re printing with a nozzle, then no matter the material you’re using — polymers, concrete, ketchup, or whatever — you can get similar errors,” Brion said. “For example, if the nozzle is moving too fast, you often end up with blobs of material, or if you’re pushing out too much material, then the printed lines will overlap forming creases.
“Errors that arise from similar settings will have similar features, no matter what part is being printed or what material is being used. Because our algorithm learned general features shared across different materials, it could say, ‘Oh, the printed lines are forming creases, therefore we are likely pushing out too much material.’”
As a result, the algorithm that was trained using only one kind of material and printing system was able to detect and correct errors in different materials on a different kind of printing system.
In the future, the trained algorithm could be more efficient and reliable than a human operator at spotting errors. This could be important for quality control in applications where component failure could have serious consequences.
With the support of Cambridge Enterprise, the university’s commercialization arm, Brion formed Matta, a spinout company that will develop the technology for commercial applications.
“We’re turning our attention to how this might work in high-value industries such as the aerospace, energy, and automotive sectors, where 3D printing technologies are used to manufacture high-performance and expensive parts,” Brion said. “It might take days or weeks to complete a single component at a cost of thousands of pounds. An error that occurs at the start might not be detected until the part is completed and inspected. Our approach would spot the error in real time, significantly improving manufacturing productivity.”
The research was supported by the Engineering and Physical Sciences Research Council, Royal Society, Academy of Medical Sciences, and the Isaac Newton Trust.
The research was published in Nature Communications (www.doi.org/10.1038/s41467-022-31985-y).